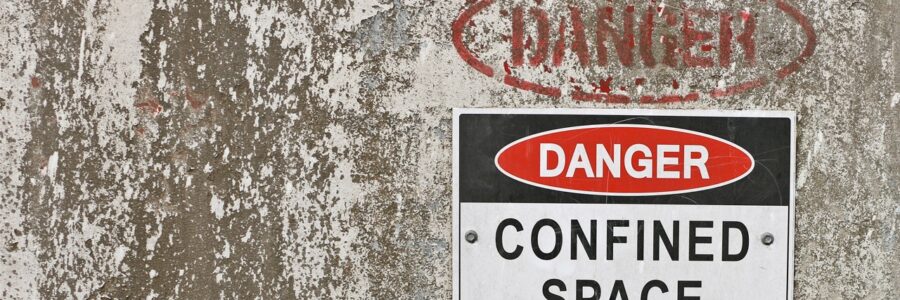
Lessons Learned from Catastrophic Cabin Creek Confined Space Incident
By Jerome E. Spear, CIH, CSP, FAIHA
According to a 2020 report from the Bureau of Labor Statistics, 1,030 workers died in confined spaces between 2011 to 2018. Each of these deaths represents a nightmare scenario in which the proper safety precautions were not taken to protect workers placed in dangerous situations.
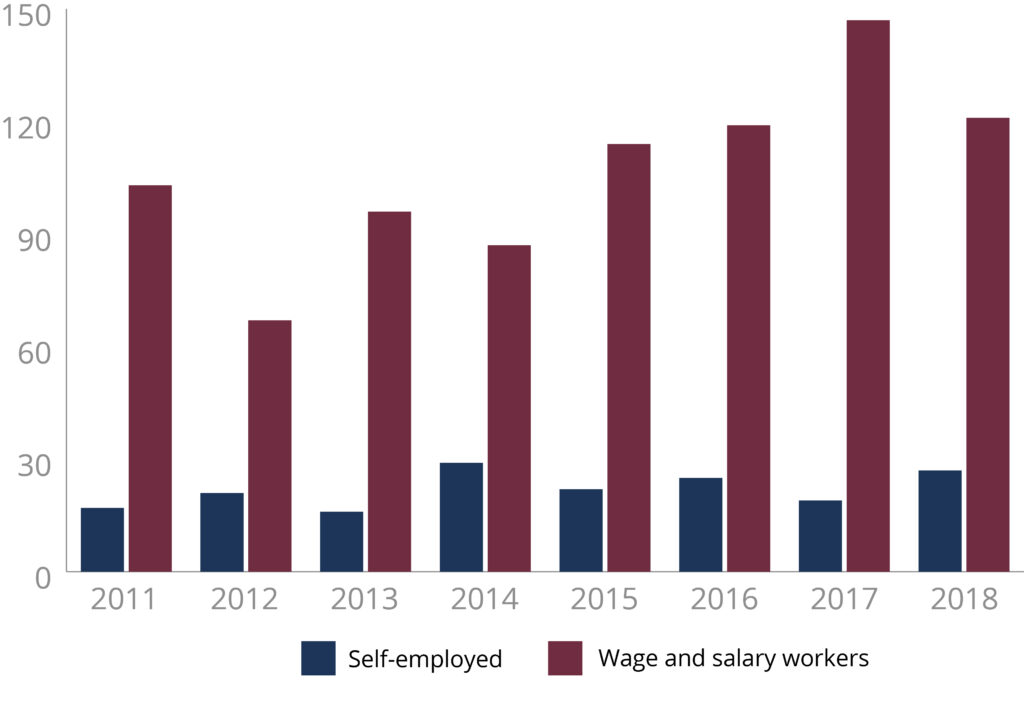
This article reviews an incident that occurred at an Xcel Energy facility 45 miles west of Denver that resulted in the death of five workers trapped in a penstock after a fire erupted. After understanding the causal factors that contributed to the fatal consequences of that event, this article will review several actionable recommendations for preventing similar incidents from happening again.
Understanding the Fatalities at Cabin Creek Hydroelectric Plant
On October 2, 2007, a hydroelectric plant in the mountains outside of Denver became the location for one of the worst confined space catastrophes in U.S. history. A 1,530-foot section of a 4,300-foot enclosed penstock (i.e., a large pipe that delivers water to hydroelectric turbines) was in the initial stages of being recoated by an industrial painting contractor (RPI Coating). After the flammable solvent ignited, five of the 11 workers were unable to reach the single exit and were unable to be rescued. They ultimately died in the penstock due to carbon monoxide poisoning. Three additional workers were injured but escaped to the single exit when the fire erupted.
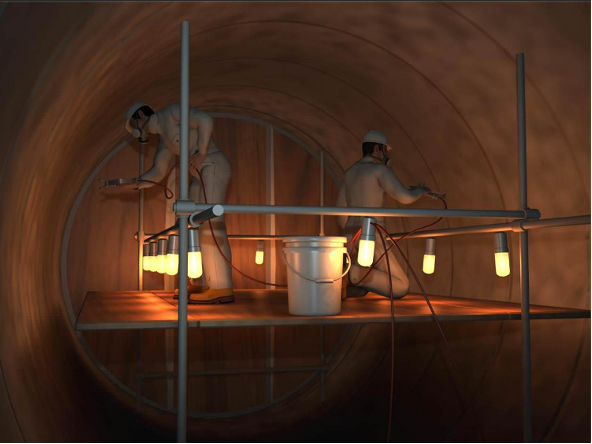
Criminal charges and civil lawsuits were filed against Xcel Energy and RPI Coating for negligence related to this catastrophe. After a review of the incident, several causal factors were identified as contributing to the incident:
- Need to flush equipment
- Use of flammable solvent
- Presence of a flammable atmosphere
- Presence of ignition sources
- Failure to fight fire
- Inability to rescue
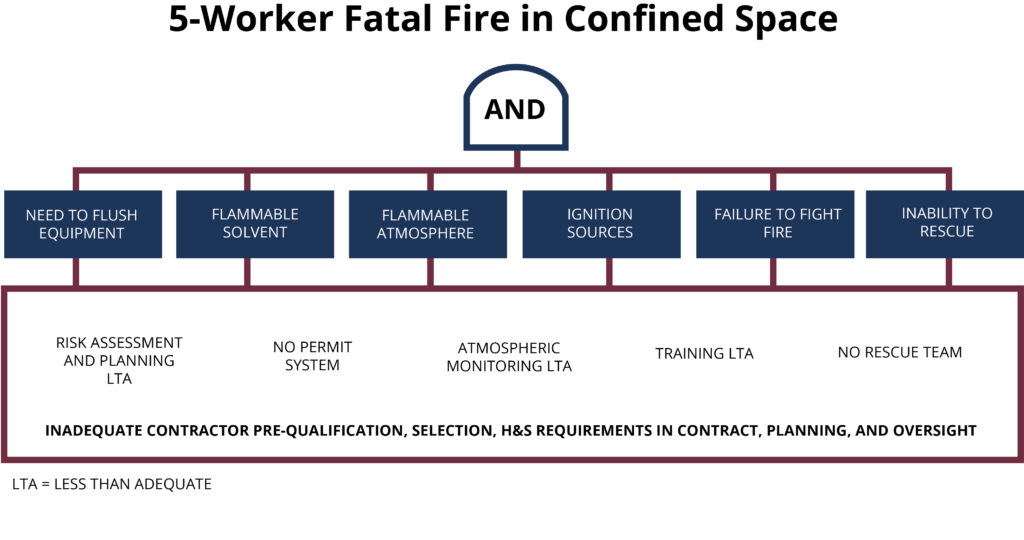
Source: Spear, AIHA Connect 2024
Many of these conditions were perpetuated by underlying conditions, including inadequate risk assessment, planning, and training. If any one of these causal factors were appropriately mitigated, then the deaths of 5 workers would likely not have occurred.
Causal Factor #1: Need to flush equipment
Because the surface and ambient temperature (54° and 58° F, respectively) during application was lower than the minimum operating temperature of the coating (60° F), the workers were consistently combatting the coating material hardening in the paint sprayer. Once mixed, the pot life of the paint was only 20 minutes before the paint began to permanently harden, which meant the workers needed solvent to flush out their equipment repeatedly.
As a result, the workers would use methyl ethyl ketone (MEK) solvent to flush out their equipment frequently. The base and hardener were being staged inside the penstock, which likely contributed to the problem they were having with meeting the minimum recommended temperature of the paint during application.
Causal Factor #2: Use of a flammable solvent
The flashpoint is the temperature at which a liquid will emit flammable vapors. There are many different solvent types, all of which have different flashpoints. In this case, the MEK solvent was selected for flushing out the equipment. MEK solvent is highly flammable with a flash point of 16° F. The solvent was stored in plastic buckets alongside a large amount of combustible paint, creating a very dangerous environment in the confined space.
Other safer solvents with a higher flashpoint could have been used instead of MEK to mitigate this risk. For example, xylene is a common paint thinner and cleaning solvent that has a flashpoint of 81° F as compared to MEK’s flashpoint of 16° F.
Causal Factor #3: Presence of a flammable atmosphere
Not only does MEK have a low flashpoint – it also has a very high evaporation rate. Due to the high concentration of MEK solvent in the air, ventilation would be necessary to protect worker safety. In this incident, the contractor failed to adequately ventilate the space.
Adequate ventilation should be assessed ahead of the project and is determined by the generation rate, ventilation rate, and the toxicity and flammability of solvents.
Causal Factor #4: Presence of ignition sources
The most likely source of the ignition was a static charge that ignited the flammable vapors from the MEK solvent. However, two other potential sources also could not be ruled out completely – 1) an electrical arc produced inside the base hopper by a stray current in the sprayer system, and 2) a hot bulb from the portable halogen lights positioned above the sprayer.
The Chemical Safety Board (CSB) determined that the most probable ignition source was static charge that ignited the explosive vapor-air mixture inside the sprayer base hopper. This is the location where one worker who was able to escape saw the initial flash. The worker was holding a non-metal reinforced hose that was connected with a metal swivel connector at the end near the inside wall of the metal hopper. After the incident, the swivel and base hopper hose could not be located, presumably consumed in the fire. However, they found remnants of an inner woven metal sheath that had belonged to the hose used to circulate MEK in the hardener hopper. Thus, the CSB concluded that the hose to the base hopper was not comprised of a metal sheath, which indicated there was no electrical bonding. Proper bonding and grounding would have mitigated this hazard. For additional information, the Bonding and Grounding article on jespear.com and featured in The Synergist (Sept 2008), provides more information on the topic.
Causal Factor #5: Failure to fight fire
No fire extinguishers were immediately available to the workers inside the penstock when the fire first ignited. The only fire extinguishers available were located outside the penstock entrance 1,450 feet away. Obviously, the workers could not reach these extinguishers when the fire started. As a result, the fire blocked five workers from escaping to the single-point egress 1,450 feet away.
Causal Factor #6: Inability to rescue
Attempts to rescue the workers were complicated by a lack of exit points. Only one exit was available to workers, far away from the application location. The emergency response plan for rescue services was to call 9-1-1. However, no emergency responders with confined space technical rescue certification were at the plant nor immediately available. The closest certified community rescue services were located 1 hour and 15 minutes away.
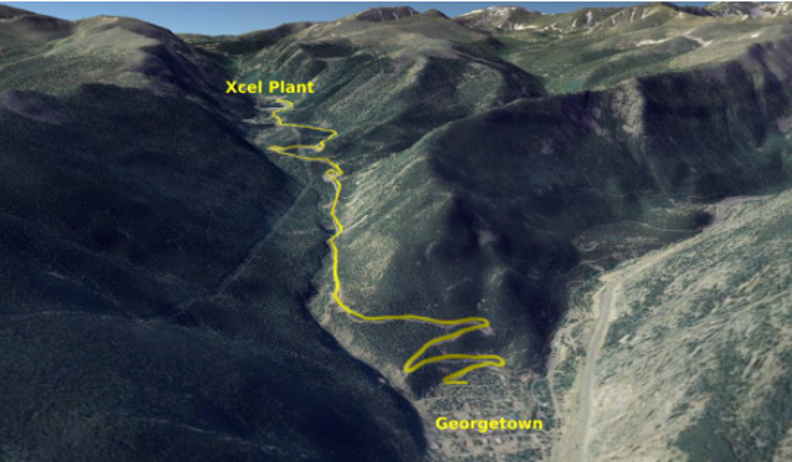
The five workers trapped in the penstock were in radio contact for 45 minutes; however, there was no trained rescue personnel and equipment, neither onsite nor within a reasonable distance of the plant to rescue the workers. There was obviously no rescue plan developed for the confined space spray painting project.
How can a premises owner improve a contractor’s safety performance?
Underpinning all these issues was inadequate contractor prequalification, selection, planning, and oversight. Liability is a complex issue, and often ambiguously defined under the legal and regulatory system. However, it is true that an ounce of proactive prevention is worth a pound of expensive cure. Managing contractors and providing oversight is the best way to avoid the negative repercussions of liability and responsibility for tragic incidents.
To improve contractor safety performance:
- Evaluate contractors through a robust prequalification and selection process.
- Clearly communicate and incorporate health and safety requirements in contract documents.
- Establish provisions for identifying hazards and assessing the risk of those hazards during the design and planning phases of the project.
- Perform work-in-progress assessments to ensure the contractor(s) are performing the work in accordance with their contractual obligations.
- Conduct post-construction evaluations to provide feedback to all parties and identify necessary corrective actions for future projects.
Prequalification and contractor selection
Typically, prequalification and contractor selection involves a prospective contractor completing a prequalification questionnaire (PQQ) with supporting documentation. The PQQ is then reviewed by a panel of experts with experience in SH&E (safety, health & environment) as well as technical, quality, and financial aspects.
From a safety, health & environmental perspective, the contractors are judged based on risk reduction practices as indicated by their responses in the questionnaire. For more information about prequalification criteria, read our article on improving contractor performance (Spear, Sept 2005).
Safety and health requirements in contract documents
Best practices for managing contractor safety include clearly communicating safety and health requirements in the contract documentation. During this process, you should identify the responsible party, list requirements for an adequate project safety plan, and list specific standards and regulations that apply to the project.
OSHA regulatory standards tend to lag behind consensus industry standards and best management practices. Having clear standards and project-specific requirements included in contractual agreements can further define roles, responsibilities, and expectations even if regulatory standards do not address site- and/or project-specific requirements.
What rules apply?
Different regulations apply to work categorized as new construction versus maintenance and repair. At the time of the Cabin Creek incident, OSHA’s regulation, 29 CFR 1910.146, Permit-Required Confined Spaces, applied to general industry worksites but not to construction sites. OSHA’s confined spaces in construction standard was not promulgated until several years after the Cabin Creek catastrophe. If the work is considered “maintenance,” which includes cleaning, inspecting, repainting, or replacing components similar to the existing tank, vessel or structure, then the OSHA general industry standards apply. When the work merely involves the repainting the structure, the issue of whether the project is a “maintenance” or “construction” activity is a bit murky and determining which OSHA standards apply is not clear-cut. Several factors should be considered, including whether the object is a one-to-one replacement, the physical size of the object being worked on, the complexity of the task, and whether the work is performed in-house or by an outside contractor, whether the work is routine or non-routine (OSHA, 1994; OSHA, May 1999; OSHA, Feb 1999; OSHA, Nov 2003; Spear, March 2005).
For the Cabin Creek repainting project, Xcel Energy and RPI Coating considered the project a construction activity, whereas OSHA determined the job to be maintenance work and cited Xcel and RPI for violations of its confined spaces standards under OSHA’s general industry rules. Regardless of the interpretation, this incident illustrates the importance of identifying and determining (during the pre-contract phase) the applicable safety, health, and environmental standards that shall apply to the project.
Prevention through design and planning
Effective prevention efforts start in the pre-planning and design phase of projects. As we can see from the Cabin Creek incident, risk assessments and mitigation recommendations were not considered upfront.
Throughout the Cabin Creek incident, inadequate attention was paid to prevention as part of the project planning and design. Minimal risk assessments were conducted prior to the project. In addition, despite potential hazards being identified by a civil engineer earlier in the year before the project began, none were acted upon. Neither Xcel Energy nor RPI Coating included the hazard assessment or recommendations aimed at reducing the risks in the project description or plan.
Finally, not all the crew members from RPI were given training prior to the start of the project.
Work-in-progress assessment and verification
Consistent and periodic assessments should be performed to verify that proper safety measures are being implemented. A key part of this effort is establishing relationships with team members and having honest discourse with stakeholders and crew members.
Very few assessments or in-progress safety verifications took place while the Cabin Creek project was ongoing. An engineering firm hired to consult on the work provided minimal safety oversight. The firm performed pre-job assessments and recorded advising the contractor on material safety data sheets. However, no records indicate that any safety recommendations were issued to prevent the above-described conditions that contributed to the incident.
Post-construction performance evaluation
Finally, evaluating the contractor at the conclusion of the project will determine if the contractor remains approved for future projects. Safety and health performance are two factors that should be accounted for in this decision-making process. Other factors to consider include, the quality of the work, meeting schedule deadlines and milestones, meeting budgetary constraints, project communications, and compliance with ethical and legal obligations. Effective contractor management takes a multi-disciplinary approach.
How to prevent history from repeating itself
The Cabin Creek incident was a devastating and tragic event that occurred because many risk factors were not mitigated upfront. If any of the identified contributors had been prevented or removed from the equation, the results would likely have been very different.
We know, from this incident, that managing and evaluating contractor safety performance is key in preventing similar incidents from happening again in the future. This includes evaluating contractors with prequalification criteria, including health and safety requirements in contractual agreements, defining proper safety procedures up front between all stakeholders, and conducting in-progress and post-project evaluations.
For more information on improving contractor safety performance, listen to our 2-part podcast series, available on our website.
References
Bureau of Labor Statistics. (July 2020). Fact Sheet | Fatal occupational injuries involving confined spaces. https://www.bls.gov/iif/factsheets/fatal-occupational-injuries-confined-spaces-2011-19.htm.
CSB.gov. (August 2010). Xcel Energy Company Hydroelectric Tunnel Fire. https://www.csb.gov/xcel-energy-company-hydroelectric-tunnel-fire/.
OSHA. (August 1994). MEMO: Construction vs Maintenance.
OSHA. (May 1999). Response Letter to J. Nigel Ellis.
OSHA. (February 1999). Response to Randall A. Tindell RE: The difference between maintenance and construction; scaffold inspection requirements; definition of periodic inspections.
OSHA. (November 2003). Response to Raymond V. Knobbs RE: Distinguishing construction from maintenance; etc.
Spear, Jerome. (May 2024). 2007 Cabin Creek Hydro Penstock Confined Space Painting Catastrophe. AIHA Connect 2024 Presentation.
Spear, Jerome. (Sept 2008). Bonding and Grounding. Synergist. https://jespear.com/bonding-grounding-controlling-static-electricity/
Spear, Jerome. (Sept 2005). Improving Contractor Performance: Keep Safety in Mind from the Start. Synergist.
Spear, Jerome. (March 2005). Confined Space Entry: A Review of Confined Space Standards Applicable to Contractors. Synergist.
